Breaking Free from Robot Programming with Motion Planning
Imagine a busy manufacturing floor. In the center of it, a robotic arm seamlessly picks and places items from a conveyor belt, dodging obstacles, adjusting to speed variations, and precisely meeting cycle-time requirements. Behind this seemingly simple task lies a complex web of programming decisions, handled by specialized robot programmers.
For years, industrial robots have been programmed using two primary tools: vendor-specific programming languages and teach pendants. But these approaches come with challenges that often lead to time-consuming programming and extensive trial-and-error. At Jacobi Robotics, we're taking a different approach with our advanced motion planning tools, designed to make robot programming more intuitive, efficient, and accessible.
The Challenges of Traditional Robot Programming
Let’s start by breaking down these traditional tools:
-
Vendor-Specific Programming Language
Think of this as a low-level language unique to each robot manufacturer. These languages allow precise control over the robot but are often complex and lack the flexibility programmers need. Every feature added requires a deep dive into the documentation, and every change means re-programming—a costly task in fast-paced production environments. -
Teach Pendant
The teach pendant is essentially a handheld device that allows programmers to guide the robot through its motions by manually “teaching” it waypoints. The robot is “jogged” through specific positions in space to define a path from Point A to Point B. It’s a little like using a joystick to set waypoints on a GPS: you move the robot to each waypoint and instruct it on how fast to move, when to stop, and how to blend movements.
But here’s where things get tricky. This programming paradigm requires the programmer to define both the “WHAT” and the “HOW” of every motion. For instance, a programmer might define the “WHAT” as “if a box is at the conveyor, move to pick position.” However, defining the “HOW” requires specifying waypoints, speeds, and collision-free paths. It’s an iterative process involving a lot of iterations through trial and error.
The Problem with the Traditional Approach
At its core, the challenge lies in robot controllers functioning like black boxes. Even for experienced programmers, predicting exactly how a robot will move between waypoints isn’t always possible. Consequently, programming can become an endless loop of testing, re-adjusting, and avoiding collisions or robot “singularities”—those quirky positions where a robot’s arm unexpectedly stalls or moves in unintended ways. And even when the robot moves as expected, achieving optimal cycle times often requires continual fine-tuning.
Motion Planning: A New Paradigm
Now imagine an alternative where the programmer only needs to define the “WHAT” and let an intelligent system figure out the “HOW.” This is the promise of motion planning.
With motion planning, instead of manually setting waypoints, the programmer provides the system with information about the surrounding environment—typically through CAD models or vision sensor data. From there, the motion planner does the heavy lifting, automatically generating an optimized, collision-free path, and can even meet specific behavior requirements, such as "keep the end effector pointing downward".
The potential of this approach is immense. Not only does it cut down on programming time, but it also minimizes the risk of collisions and improves the robot’s productivity by optimizing its path.
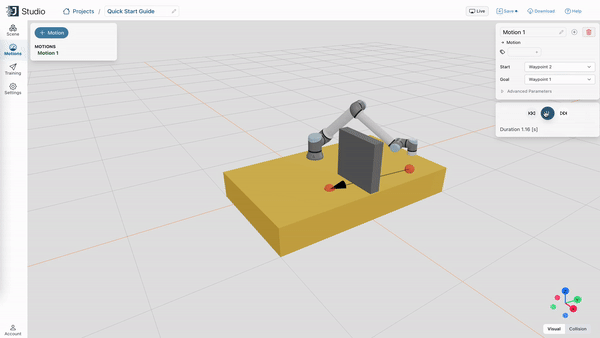
How Jacobi Robotics is Redefining Robot Programming
At Jacobi Robotics, we’re building on the power of motion planning to revolutionize robot programming. Our state-of-the-art motion planner is designed to generate real-time optimized motions, meaning that programmers no longer need to tediously define waypoints or adjust motion parameters. Instead, they simply set the robot’s task, and let Jacobi take it from there, from calculating the most efficient motions, to simulating it and eventually executing it on the real robot.
The benefits of this shift are substantial:
- Reduced Programming Effort: The motion planner does much of the heavy lifting, so programmers can focus on defining tasks instead of paths.
- Increased Productivity: With optimized paths and collision-free movements, robots can work faster and more effectively, improving cycle times and throughput.
- Configurable Applications for Non-Programmers: By automating the “HOW,” motion planning makes it possible for non-programmers to configure tasks, eliminating the need for a robot programmer for every small update.
- Adaptability to Dynamic Environments: Traditional programming struggles in environments where conditions change frequently. Motion planning, on the other hand, allows robots to adjust paths in real time, responding dynamically to changes in the environment.
Imagine the impact on industries from manufacturing to logistics, where robots can autonomously adjust to fluctuating production demands or unexpected obstacles.
Moving Forward with Jacobi Robotics
The future of robot programming is about making robots more accessible without sacrificing efficiency or reliability. With Jacobi’s tools and solutions, robot applications can be configured and deployed faster, with fewer resources and less downtime, opening up the potential for automation in new and complex environments.
If you’re interested in exploring the future of robotic programming, visit us at www.jacobirobotics.com, or follow us on LinkedIn and X to learn more about our tools and solutions.
Blog overview