Industrial Robotics: From Programming to Configuring Robot Applications
In the world of industrial robotics, traditional programming methods have long been the norm. However, recent advancements in robot motion planning technology have transformed the way we interact with robot applications. Leveraging the power of motion planning, engineers can now shift from complex programming tasks to a more intuitive and efficient process of configuring robot applications. Let's explore how this transformation is revolutionizing the industrial robotics landscape.
Streamlining Configuration. Traditionally, programming industrial robots involved writing code specific to each robot and task. This process required expertise in a variety of robot programming languages, such as RAPID, Karel, UR Script, INFORM or KRL, and extensive testing to ensure precise movements. However, with the advencements in robot motion planning, engineers can now configure robot applications using intuitive interfaces in no time. These methods leverage 3D models of the robot environment for collisions avoidance, allowing the user to merely configure the start and end robot poses, and add limits on the gripper orientation or speed if the robot is carrying a heavy payload.
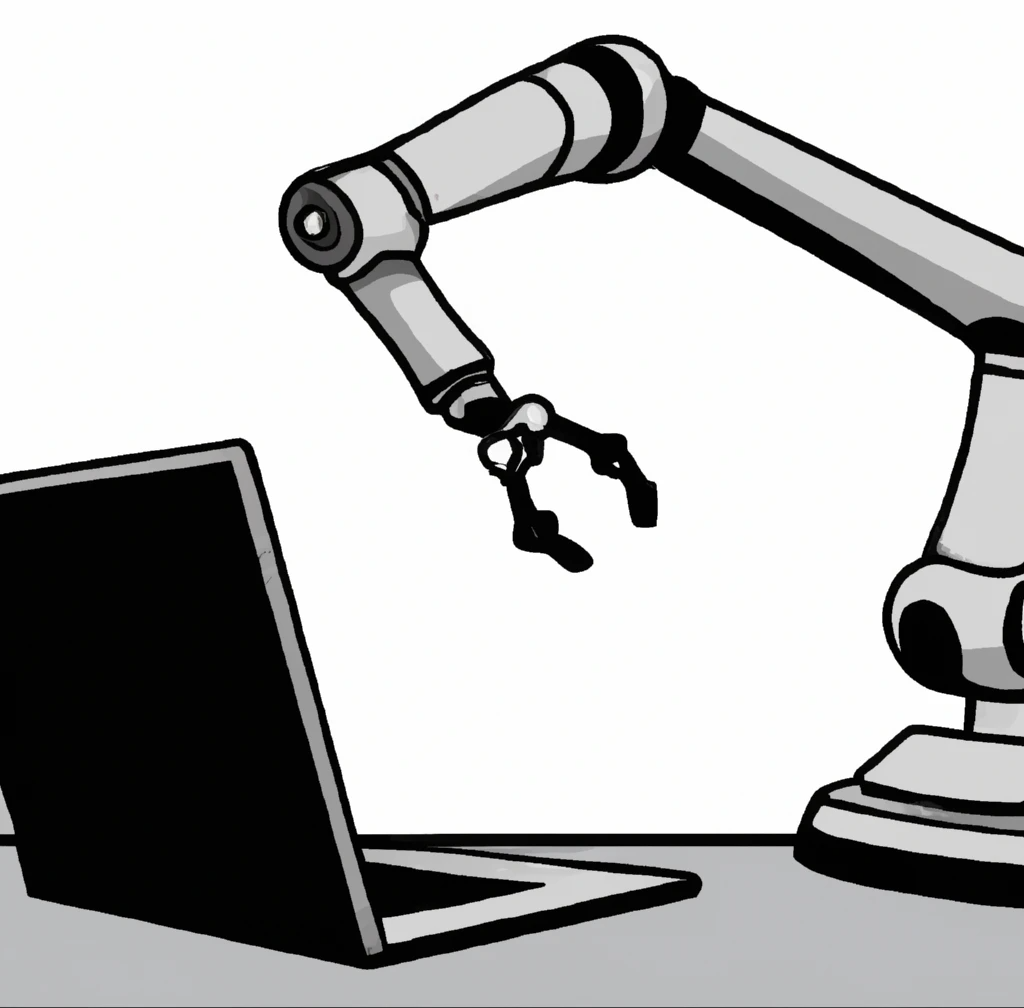
Fast and Efficient Planning. With robot motion planning, engineers can define the desired motion of the robot and automatically generate optimized trajectories. Instead of spending days manually iterating over different velocity and acceleration profiles to reduce cycle times, this technology takes into account factors such as reachability, joint limits, and obstacles in the robot's environment to ensure safe and efficient motions, reducing the time and effort required for programming from days to hours.
Flexibility and Adaptability. With the traditional programming approach, making changes to robot tasks or adapting to new requirements often involved rewriting code and extensive reprogramming. Robotics programmers can spend days to repurpose a robot from one product line to another for machine tending or configuring additional pallet patterns in robot palletizing. However, by configuring robot applications through motion planning, engineers can easily modify robot applications and adapt to changing production needs. This flexibility enables quicker response times and seamless integration into dynamic manufacturing environments.
Improved Productivity and Cost Savings. By leveraging robot motion planning, industrial automation providers can significantly enhance productivity and reduce costs. The streamlined configuration process reduces development time, allowing for faster implementation of robotic solutions. Additionally, the intuitive programming interfaces and automation capabilities minimize the need for specialized programming expertise, reducing training requirements and associated costs.
The paradigm shift from programming industrial robots to configuring robot applications through motion planning marks a significant milestone in the evolution of industrial robotics. This transformation empowers engineers to streamline configuration processes, improve flexibility and adaptability, and ultimately drive productivity and cost savings. As the industrial robotics industry continues to advance, embracing motion planning technology will play a pivotal role in unlocking the full potential of automation.
Are you ready to give robot motion planning a shot? Try the Jacobi motion library Here.
Blog overview